
Rapid Prototyping
3D printing has become an integral part in the design process making concepts to become reality with relatively low costs
Covid-19 Geiger development
Rapid prototyping has become an integral part in the design process. Speeding up and reducing the time needed for finalising a product during the development stage. Below is a selection of images from this process for the Covid-19 Geiger.
Rapid Prototyping Process
My 3D Printer
Rapid prototyping has become an integral part of the design process. Speeding up and reducing the time needed for finalising a product during the development stage. Below is a selection of images from this process for the Covid-19 Geiger.
Flexi-filament
Flexi-filament played an essential part of this design process. Though not perfect, as a design tool, it quickly became invaluable as I became aware of how the band was interacting with the user's wrist and the Covid-19 Geiger—resulting in adjustments needing to be made to increase the need for an improved framework within the construction of the strap.
Beginning Alterations
During development, it quickly became apparent that the band's complexity had to be reduced meaning that a steel band similar to one in a tape measure would be embedded into the straps. Eliminating the need for a clasp.
Initial Prints
Tollerances
As I was designing the interior components for the band, it was essential to understand the placement of each element and allow for accurate tolerances. This model was printed at 2.0 scale.
Buckle Had To Go
Originally designed to have three elements making up the band. Quickly it came apparent that the clasp was too fiddly for people, especially with restricted hand dexterity to use.
Three Elements
Initially, the Covid-19 Geiger was to consist of three main components, these were.
The main unit
Band
Press in buckle.
The latter had to be removed. This was due to the clip being to fiddly to use, to combat this the band now comes with an embedded metal strip that will wrap around the user's wrist.
Further Development
Constant Development
After picking a design and taking it forward to be rapid prototype. I realised that the practicality of the design would have to change, this was down to my lack of knowledge on the flexi-filament and how it would interact with the users wrist and’s wrist and hold the main body of the band.
Seal Failures
This was one of the final designs that would eventually be developed into the final COVID band. Alterations had to be made as you can see the band didn't keep a consistent seal around the main body of the band.
Development
This was an alternative strap design. Though I did like the aesthetics of the band, practically the band was unable to keep the main body of the watch in place consistently. Maybe with an embedded frame, the body could stay in, but as this was to reduce the overall cost of the watch the design had to be altered.
Finalising The Design
Development
This was the development of the previous band. Once again the band worked to an extent but would require further development. The body of the watch was going through alterations at the same time as the band and creating an appropriate tong and groove element between the two. This design was also focusing on a two-button body. However, to reduce cost, I decided a single push button was the best option.
Finalise
Though I liked the design of the band, I felt that the design was not playful enough and would need adjustments that would not only keep the main body of the watch secure but also be aesthetically pleasing.
Final Design
These two were the final alterations of the band design. I decided to focus on the band at the forefront of the design. The design overall seemed very minimalist, though, through this minimalism, the overall cost of the design is overall reduced.
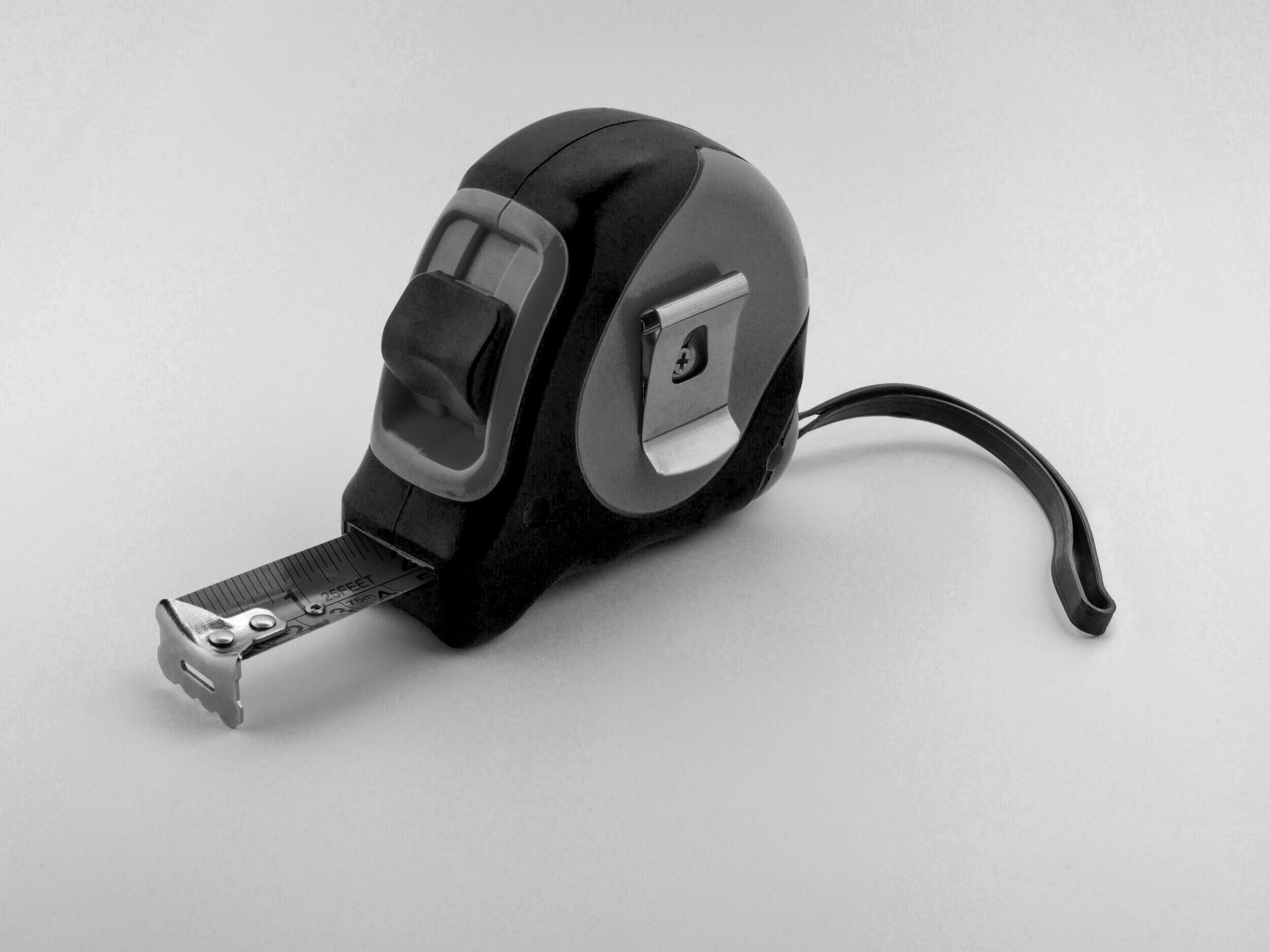


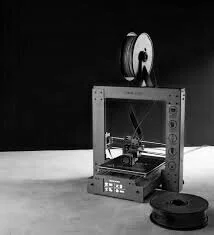



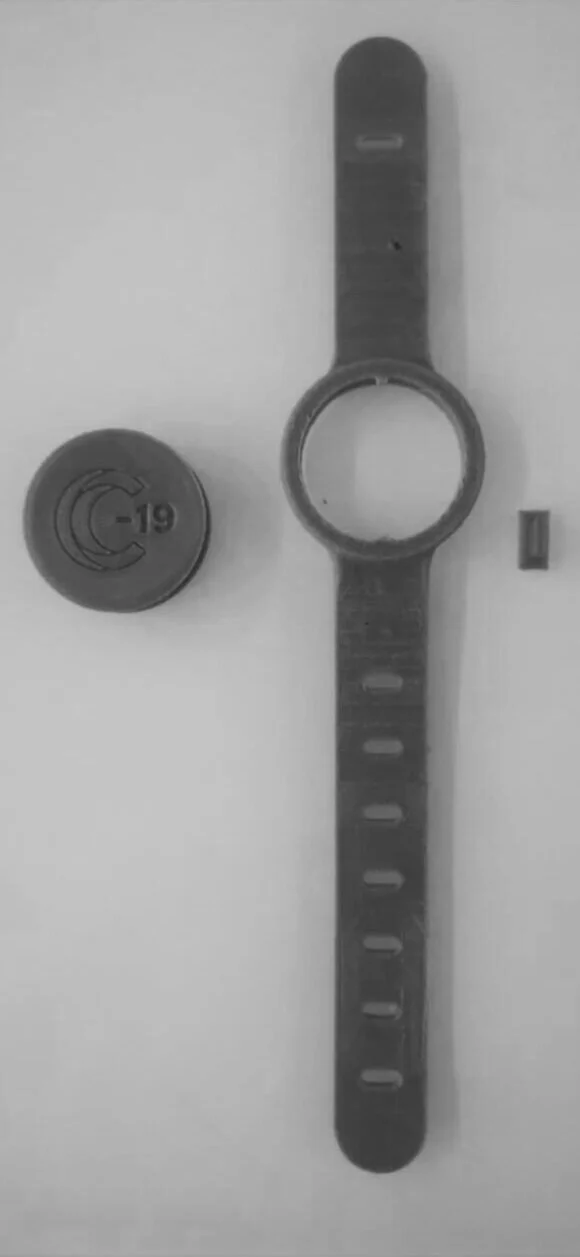

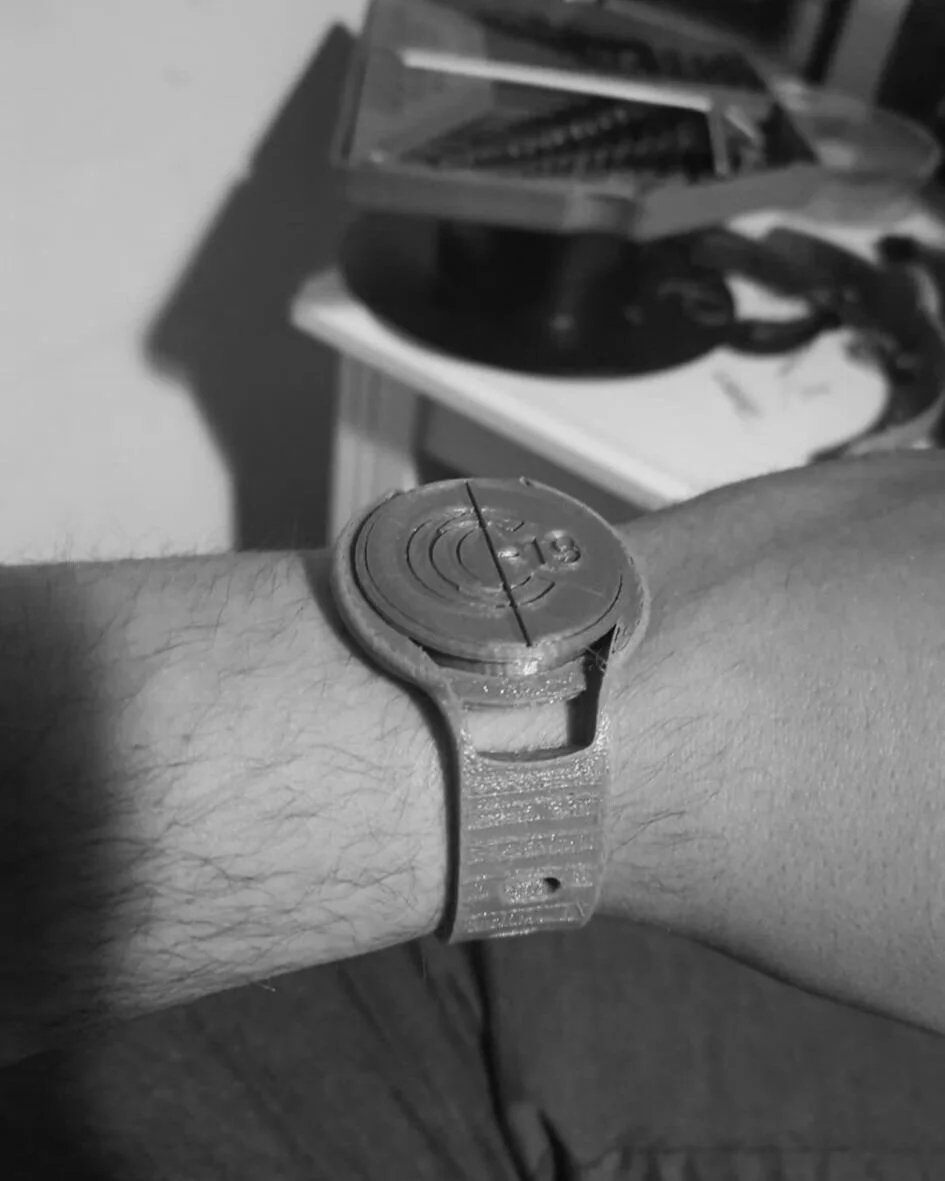

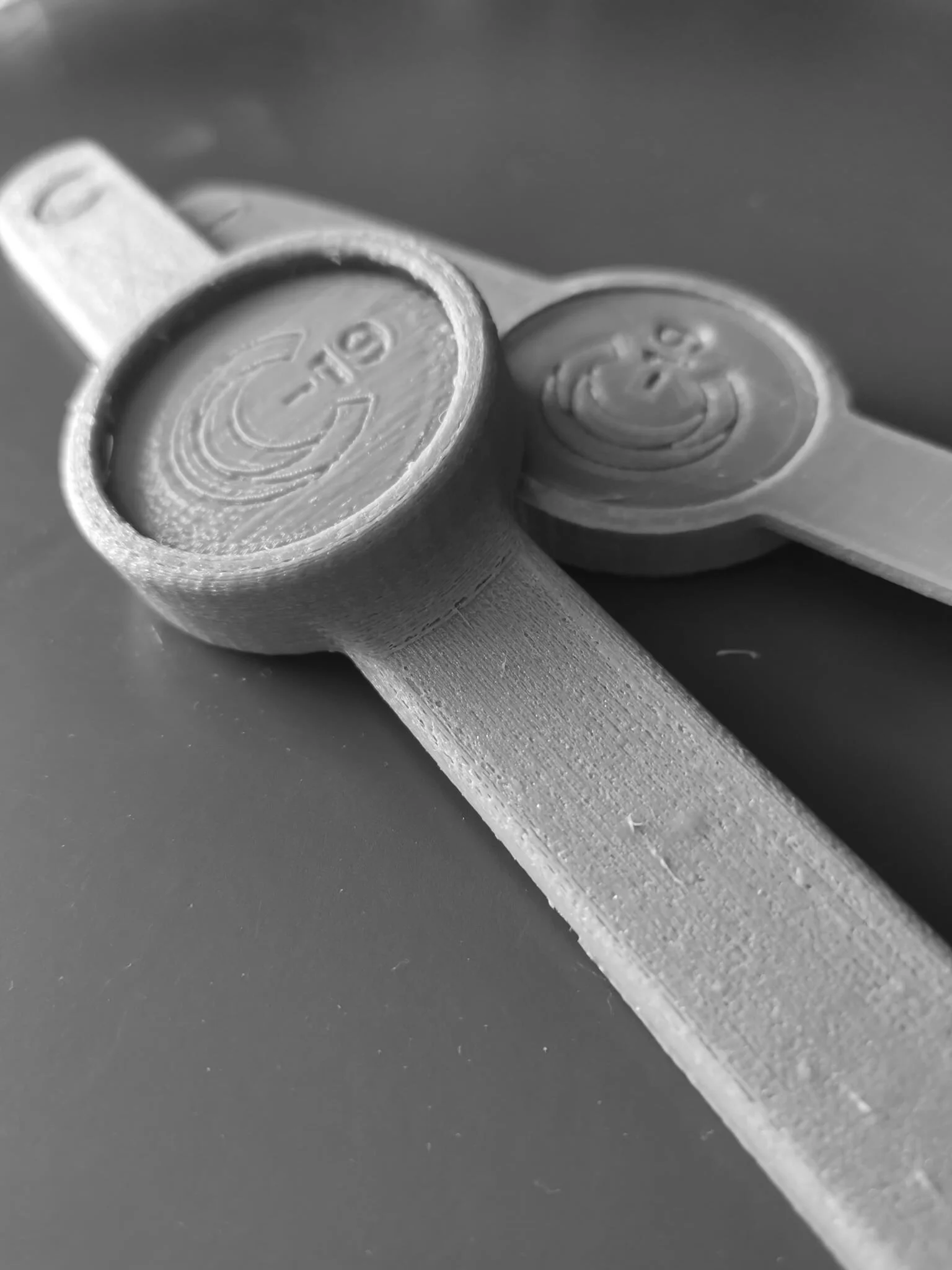